The last year or so has presented multiple challenges across all industries for different reasons but something that has been causing big problems is the global chip shortage issue we are facing. HiddenWires’ US correspondent, Michael Heiss looks at what that means for the next year and beyond.
At this time of year everyone is looking forward to the forthcoming “holiday season”, albeit different things for different people. Of course, kids (and those of other ages, as well) are dreaming about their presents. Shoppers are waiting to see what the deals will be for “Black Friday”, Boxing Day and the various “Deal Days” from the traditional and online retailers across the globe.
At the same time, to support those dreams and wishes, people on the supply side of the fence, including those reading this article, are also looking forward to it, albeit as we will soon see, with some trepidation. After all, the fourth quarter is the season when many tradespeople earn their profit. Indeed, there are many origin stories for the phrase “Black Friday”, and the one that appears to be the oldest is from 18th century Philadelphia when the police used it to describe the increased street traffic by shoppers. More recently, it has popularly been said to describe holiday shopping as the period that turns the red ink (or spreadsheet entries) into black to signify the year will be profitable.
Putting all of that together for us has often meant a variety of things: assembling sales bundles, creating ads and social media activities, and most importantly, making certain that you have sufficient stock of the correct items that will be in demand in any given year. Normally, that is a scheduled activity, but, unfortunately, this year it will be different.
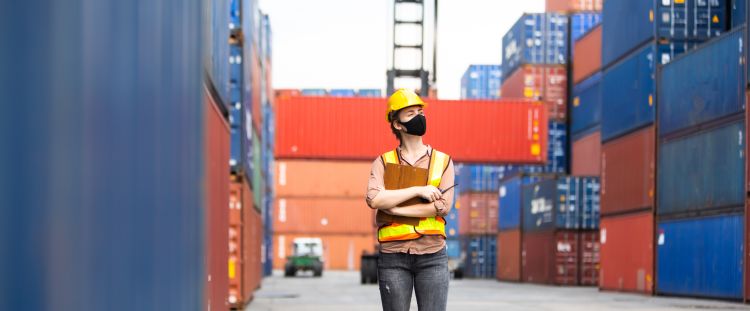
Covid-19 has delayed container ships being loaded and unloaded at shipping ports around the world. BigPixel Photo / Shutterstock
For anyone who has been in this business for more than a second knows that should be a normal activity. By now you, and equally important, your clients and prospects have undoubtedly seen, heard, or read something about a “chip shortage” in the popular, business and trade press. No, we’re not talking about “chips” with your fish, or the chips that we Americans use with dips while watching our version of football. There is much more to the story than the general reporting. If it hasn’t already, this will almost certainly impact your business in the fourth quarter and likely well into the year ahead.
Let’s put the conclusion first, then explain how it was reached, and then circle back around to some ideas as to how to deal with all of this. It’s easy to say that “stay home” orders and similar things related to Covid-19 are to blame. Yes, to some extent. Factory closures due to fear of infection spread has meant the inability of chip foundries to meet their order demand. But, even in what was a slowdown in various economic statistics, some things have grown significantly.
“If it hasn’t already, this will almost certainly impact your business in the fourth quarter and likely well into the year ahead.”
That leads to problems in our industry. After all it wasn’t just people stocking up on toilet paper and such, but a huge demand for webcams, monitors and laptops to support all the people who suddenly had to work from home. Add to that the laptops and headphones needed for distance learning education when schools were closed. Those electronics products had to come from somewhere, and even if factories were cranking things out at full speed, which they couldn’t, we would still have shortages. And that, we did!
Remember the switch over the past few decades to “just in time” (JIT) manufacturing? That means that both parts suppliers, manufacturers and those along the various supply chain channels tried not to stock much more than what the forecast was for a few weeks. Great if demand is as projected, but not so hot when you make laptops or audio devices and suddenly find the market demand well beyond your expectations. Great for sales, but not so much if the factories could not produce. Add in the issue of not being able to get the parts you need because of closures and things sink quicker than the Titanic hitting an iceberg.
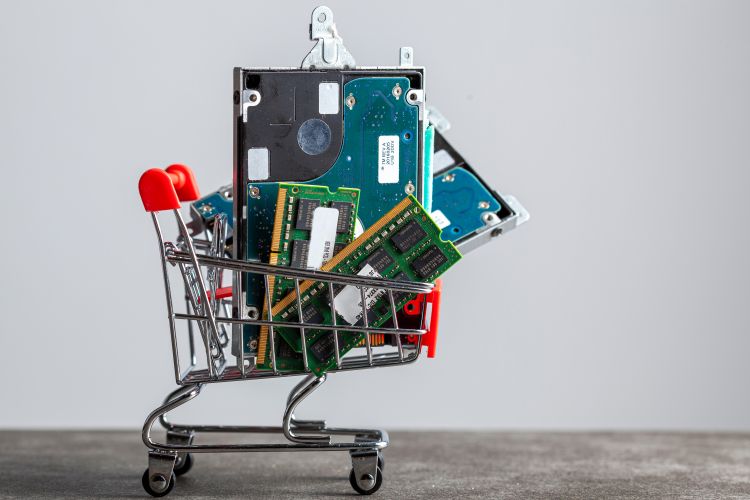
Chip shortages are causing supply issues across many different industries. Grandbrothers / Shutterstock
Parts shortages, particularly for audio products, have been exacerbated by a fire last October at the factory of a major Japanese manufacturer of key components such as high-end DACs. As of now, the factory is not back online and very few parts appear to be available from the company’s alternative production sources. Sure, manufacturers keep safety stock, but in a JIT environment they run out quickly. Add in the increased demand and one has a “perfect storm” situation.
Fine, you’ll say. Why not just use other parts. That’s not as easy as it sounds. Any replacement part requires design, prototyping, testing, safety, and emissions certification and more. That all takes time. Add in the fact that the replacement parts, themselves, may suffer from shortages and you have a “Catch-22”. Yikes!
OK, let’s go down a different road, or in this case, a different sea. Let’s say that a manufacturer does not have any chip shortages. Great, but the same production issues impact the supply of the complex, high-value parts where the companies have to fight with demand from auto manufacturers and others. Small “jelly bean” parts such as resistors, capacitors, diodes and more simplistic processors are also on short supply.
One more non-chip part issue is a less obvious one: metal. Prices have gone up for copper, which impacts things such as transformers and the sheet metal used for heat sinks, chassis parts and front- or rear-panels. Even if the producers are able to get them on time, the price will almost certainly be higher. Price increases roll down hill, but more about that in a few lines.
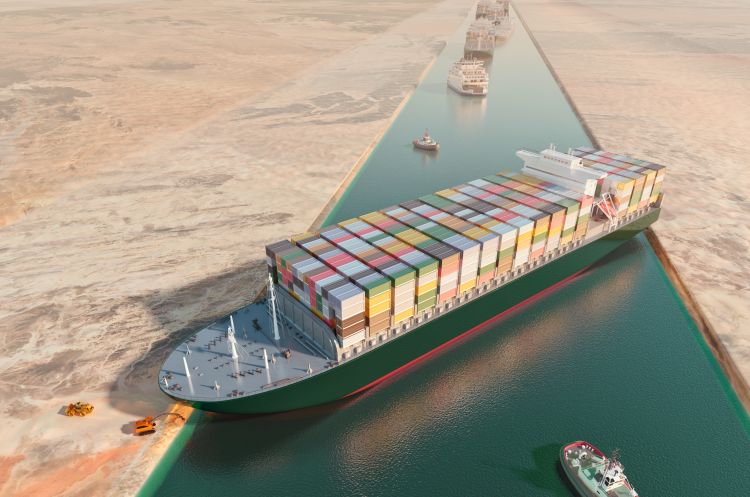
The blockage of the Suez Canal has also contributed to problems. Corona Borealis Studio / Shutterstock
Ah, but as they say in the late-night infomercials, “But WAIT, there’s MORE!”. For a moment let’s forget about getting products made. Another part of this supply chain puzzle is getting products from China and other Asian manufacturers to the various markets across the globe. After all, having goods but not being able to ship them is like the proverbial tree falling in the forest that no one hears, so one asks if it really fell. Same thing here.
First, it was the stoppage in the Suez Canal when that enormous cargo ship blocked the passage for a week or so. Then, at both the ports in Asia and in the US and Europe, the ports were short staffed or even closed for a while due to workers not able to come to work. According to the local media here in Los Angeles there are now over 75 ships waiting off the Port of Los Angeles/Long Beach, the busiest port in the US. The same thing is the case at major container ports in the US and Europe.
“Any replacement part requires design, prototyping, testing, safety, and emissions certification and more.”
That, in turn, takes another piece away from our supply chain puzzle that prevents it from being completed. If the ships can’t be unloaded, the containers can’t be emptied. If they can’t be emptied, they can’t be sent back to be filled with more goods. That, in turn, clogs up the Asian ports. Some friends of mine had their goods waiting over two weeks to get a container to load, another week or so to get it on a ship, and then an ocean crossing that took four weeks, rather than ten days to make it over. Adding one more bit of fuel to the supply chain fire, trucks and their drivers are in short supply due to all these complications, making it difficult to get the goods from the ports to the warehouses.
A concrete example before switching to some things you can do about this that will also serve as an interesting example of how all of this extends to almost every aspect of the consumer and industrial market. It is not just about “chips”. Appropriate to this time of the year, there was a story on the local news here recently about how all the circumstances just described are impacting the price of artificial Christmas trees. That’s right, Christmas trees! A standard size artificial tree will double in price this year, up to about $500 USD. Talk about the proverbial lump of coal in your stocking! It’s a bit early to see what the prices will be for natural trees, but given labour shortages, petrol pricing and other issues on the transportation market, you may only be able to get a smaller tree this year and you’ll likely pay more for it. Then again, there may be fewer presents due to all of this and the fact that what you will put under the tree will be most costly.
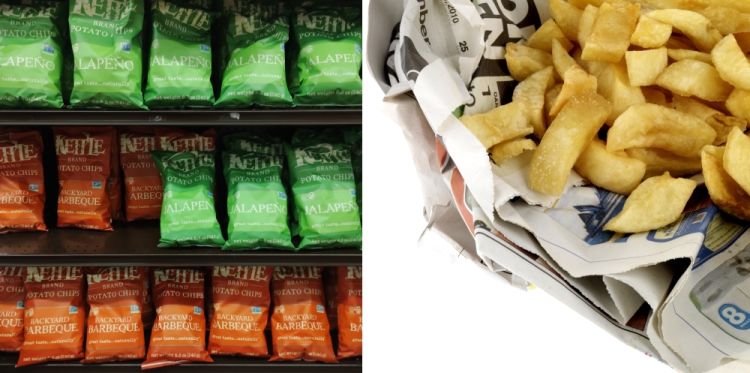
Not these chips... ...nor these
Looking at all of this, let’s circle around to what we have, why we have – or DON’T – have it, and what to do about it. First, when people ask you why you can’t deliver products on time, hopefully all of this narrative will allow you to give a better view of the “why”. Giving clients and customers a true and honest answer is sometimes the most important thing.
Now, what are the local impacts and how do you deal with this at ground level? First, it goes without saying that you need to review any client bids or commitments. No matter what the scope of work is, there is a fair chance that one product you need will not be there when you need it. Make certain that you are aware of any penalty charges for late job completion and do your best to see if the client understands. If not, ask an expert to see if your “force majeure” clauses cover you. You DO have that in your contracts, don’t you?
Next, it’s a given that almost anything and everything will be late. My wife and I recently ordered new kitchen appliances. Great, but good luck planning the installation. Hopefully, the fridge and range ordered in August will be here for holiday dinner preparation, but we’re not holding our breath. Maybe the range in time for the Thanksgiving turkey and the fridge to cool the bubbly for New Year celebrations. Then again, maybe not.
This may be more of a North American thing, but it does bring up yet another unexpected difficulty these delays cause. Here in the US the manufacturers, particularly for appliances, offer rebates along the lines of “buy three and get a card with 5% back, buy four and get 10% back”. Fine if you purchase the things within the promotion timing, but to get the rebate one needs not only the bill of sale, but also the units’ serial numbers. Oops, that’s another Catch-22. What if you buy and pay in time but the delivery takes place after the promotion is over? If your suppliers offer these types of deals please see if they understand the problem just played out and make certain that you don’t end up on the hook for a promise that the brand made, but which you can’t help the customer keep. That is exactly what my dealer did.
Let’s boil all of this down to action points. First, for all the reasons set forth above, this is going to be a rough (more than) couple of months for everyone in retail and their customers. Despite efforts to build new chip foundries in the US and EMEA, as well as in Asia, the best guess is that this won’t ease up until mid-2022 at the earliest; well into 2023 at the worst. Again, not just the products in our venues, but cars, appliances, clothes, furniture and almost anything that isn’t made 100% from totally local parts and raw materials. Does it take more than the fingers on two hands to count that? You don’t even need to take off your shoes and socks to count with your toes.
“No matter what the scope of work is, there is a fair chance that one product you need will not be there when you need it.”
First, keep in constant touch with your key vendors as to their delivery dates. Then, make certain that there will not be any price increases. The likelihood is that there will be. Particularly for sole-source products, keep your customers updated and make certain that your promises and contracts don’t cause you any legal or customer relations problems when the inevitable happens. It WILL. If it doesn’t, next time I’m able to travel over to the UK or EMEA for an industry event, the “chips” are on me.
Next, despite your well-meant loyalty to current vendors, this is one time when you may want to see if there are other brands and models that fit the job spec. This isn’t an issue of discontent with the brand but is just the reality of business in these times. Note of caution: particularly for products such as AVRs or surround processors where the DAC part issue is part of the problem, don’t expect that there will be an easy alternative.
I’ve already mentioned pricing. Economics 101 lays out the law of supply and demand, and don’t be shocked to see how that influences your pricing as well as retail. There are two forks in that road. One is to make certain that you don’t end up having to provision something for a job where the cost has increased beyond what you need for suitable profit. No easy answers to that one.
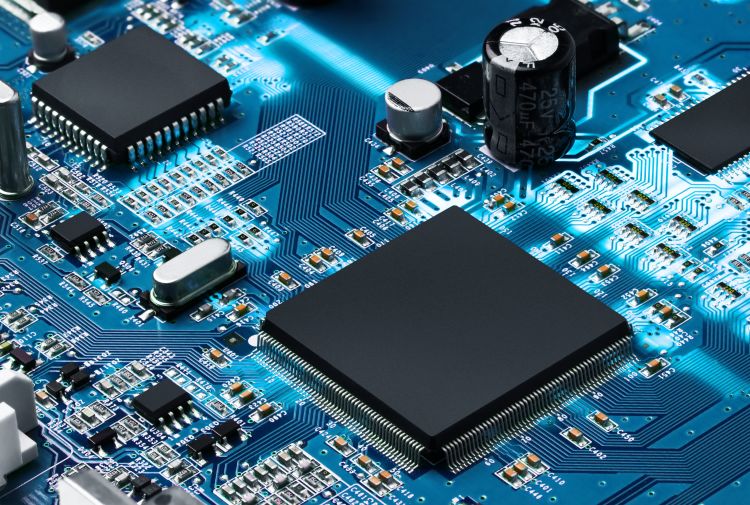
Volodymyr Krasyuk / Shutterstock
The other fork in the road is planning your own bids, adverts and promotions. As I write this in late September, I have to wonder what the “door buster deals” will be for year end sales. I’m guessing that they might not be as good as in past years. More to the whole point here, don’t forget disclaimers such as “supplies may be limited” in any public facing communication. Sometimes people accuse retailers of saying that to increase store traffic. This year it won’t be made up; it will be a fact.
The bottom line for all of this is that the “chip shortage” is more than that. It is a multi-faceted global supply chain and logistics nightmare. Hopefully this background will give you the behind-the-scenes reasons why this is all taking place along with some starter thoughts as to how to adapt to it. Face it: we all have no choice.
A final note for the year: My wishes to you all that one thing that will NOT be in short supply in 2022 is happiness, prosperity, peace, and more importantly lately than ever, health. Let’s put the past year or two behind us and work together for a brighter year ahead.
Main image: Olga Miltsova / Shutterstock