Researchers at the University of Cambridge have led a team to develop a method that can weave flexible displays and smart fabrics on inexpensive machines.
Last year the international team of academics produced a 46-in woven demonstrator display and now say they can cheaply make products in any shape or size. The smart textiles created with this approach can incorporate LEDs, sensors, energy harvesting and storage.
Working in partnership with textile manufacturers, the team produced test patches of smart textiles of roughly 50cm x 50cm, although this can be scaled up to larger dimensions and produced in large volumes.
Dr Sanghyo Lee from Cambridge’s Department of Engineering is the first author on the research paper that details the findings. “We could make these textiles in specialised microelectronics facilities, but these require billions of pounds of investment,” he said. “In addition, manufacturing smart textiles in this way is highly limited, since everything has to be made on the same rigid wafers used to make integrated circuits, so the maximum size we can get is about 30 centimetres in diameter.”
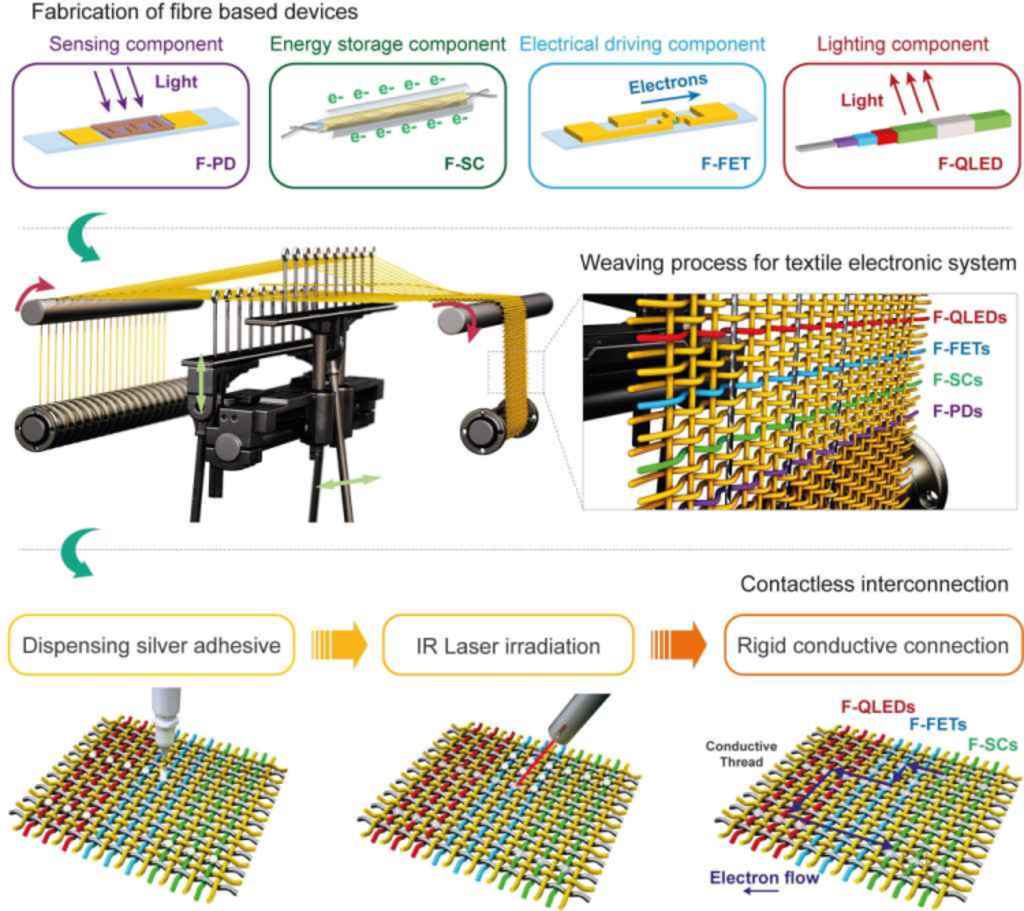
Image credit: Sanghyo Lee
Dr Luigi Occhipinti, also from the Department of Engineering, who co-led the research, added: “Smart textiles have also been limited by their lack of practicality. You think of the sort of bending, stretching and folding that normal fabrics have to withstand, and it’s been a challenge to incorporate that same durability into smart textiles.”
“These companies have well-established manufacturing lines with high throughput fibre extruders and large weaving machines that can weave a metre square of textiles automatically,” said Lee. “So when we introduce the smart fibres to the process, the result is basically an electronic system that is manufactured exactly the same way other textiles are manufactured.”
The researchers say it could be possible for large, flexible displays and monitors to be made on industrial looms, rather than in specialised electronics manufacturing facilities, which would make them far cheaper to produce. Further optimisation of the process is needed, however.
The research was supported in part by the European Union and UK Research and Innovation.
Top image credit: Alba_alioth/Shutterstock.com